現(xiàn)代制造業(yè)對(duì)"小批量、多批次"生產(chǎn)模式的需求,推動(dòng)著機(jī)器視覺(jué)系統(tǒng)從單一檢測(cè)工具向柔性生產(chǎn)中樞演變。在產(chǎn)品質(zhì)量檢測(cè)環(huán)節(jié),傳統(tǒng)AOI設(shè)備受限于預(yù)設(shè)規(guī)則的剛性框架,難以應(yīng)對(duì)新型缺陷的識(shí)別挑戰(zhàn)?;谏疃葘W(xué)習(xí)的視覺(jué)系統(tǒng)通過(guò)構(gòu)建多層卷積神經(jīng)網(wǎng)絡(luò),在每當(dāng)發(fā)現(xiàn)未知缺陷特征,會(huì)自動(dòng)生成標(biāo)注任務(wù)流,形成"發(fā)現(xiàn)問(wèn)題-學(xué)習(xí)特征-預(yù)防風(fēng)險(xiǎn)"的產(chǎn)品質(zhì)量閉環(huán)管理。
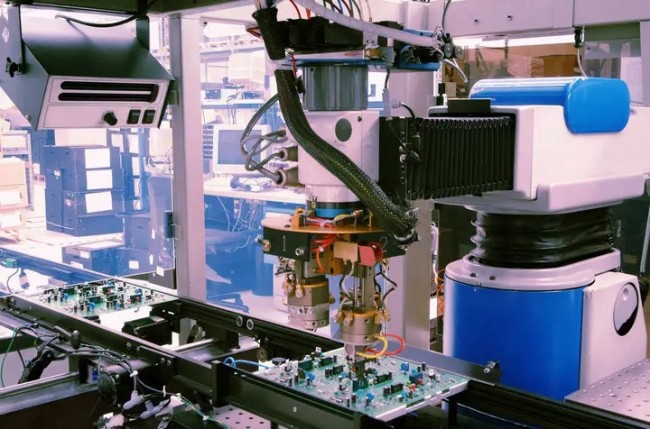
深圳虛數(shù)將將DLIA工業(yè)視覺(jué)系統(tǒng)與某汽車零部件工廠的MES、ERP系統(tǒng)深度集成,構(gòu)建起跨維度的質(zhì)量追溯體系。當(dāng)視覺(jué)終端捕捉到變速箱殼體毛刺超標(biāo)時(shí),不僅觸發(fā)即時(shí)分揀指令,同時(shí)將工藝參數(shù)偏差同步推送至加工中心,在30秒內(nèi)完成刀具補(bǔ)償參數(shù)的自動(dòng)修正,將質(zhì)量管控從末端攔截轉(zhuǎn)變?yōu)檫^(guò)程干預(yù),缺陷攔截節(jié)點(diǎn)平均移至前個(gè)工序段。
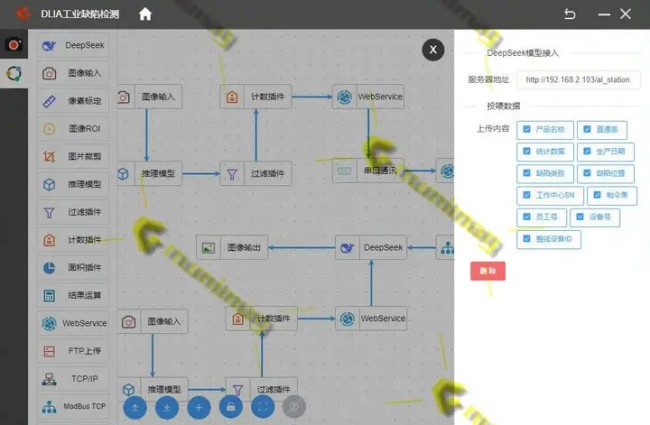
在機(jī)器視覺(jué)與人工智能的協(xié)同作用下,工廠正演變?yōu)榫邆渖窠?jīng)反射弧的有機(jī)體。當(dāng)視覺(jué)傳感器捕捉到注塑件縮痕時(shí),DLIA工業(yè)視覺(jué)系統(tǒng)不僅追溯模具溫度曲線,還會(huì)聯(lián)動(dòng)供應(yīng)鏈系統(tǒng)分析原料批次特性。通過(guò)實(shí)踐表明,這種跨系統(tǒng)協(xié)同可提升不良品根本原因分析效率。更深遠(yuǎn)的影響在于,持續(xù)積累的視覺(jué)數(shù)據(jù)正在訓(xùn)練出行業(yè)級(jí)的知識(shí)圖譜,使制造系統(tǒng)獲得類似"經(jīng)驗(yàn)直覺(jué)"的決策能力——當(dāng)檢測(cè)到新型材料表面波紋時(shí),能自動(dòng)匹配歷史數(shù)據(jù)庫(kù)中的相似案例的工藝調(diào)整方案。
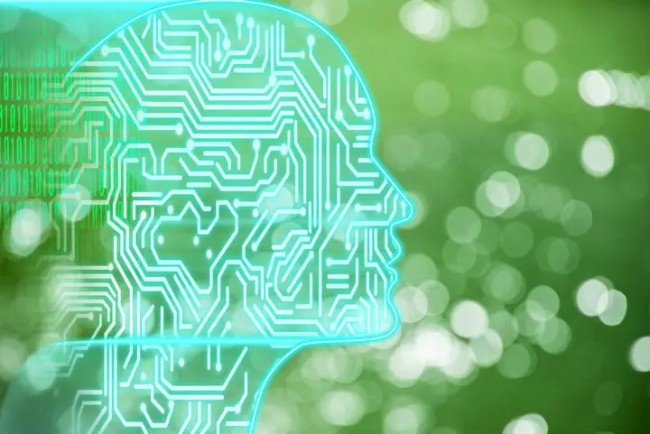