人工目檢作為工業(yè)史上沿用最久的質(zhì)量控制手段,其局限性在當代制造業(yè)中愈發(fā)凸顯。首先,人眼的分辨能力存在物理上限,難以捕捉微米級缺陷或高速運動中的異常;其次,質(zhì)檢員的疲勞、情緒波動及經(jīng)驗差異直接影響判斷的穩(wěn)定性,導(dǎo)致漏檢、誤檢率居高不下;再者,面對復(fù)雜多變的缺陷類型,人工目檢缺乏可量化的標準與實時反饋機制。這些缺陷在精密制造、電子元器件等高附加值產(chǎn)業(yè)中尤為致命。隨著深度學(xué)習(xí)技術(shù)的突破,以DLIA深度工業(yè)視覺檢測為代表的動態(tài)智能監(jiān)測系統(tǒng),正顛覆人工目檢的底層邏輯,推動產(chǎn)品缺陷目檢從“經(jīng)驗依賴”向“數(shù)據(jù)驅(qū)動”跨越。

當前的流水線產(chǎn)品的缺陷動態(tài)智能監(jiān)測核心理念在于通過實時數(shù)據(jù)采集、智能分析與決策閉環(huán),構(gòu)建覆蓋全生產(chǎn)鏈的主動式質(zhì)量管控體系。在動態(tài)監(jiān)測場景中,DLIA系統(tǒng)通過高幀率工業(yè)相機實時捕獲流水線產(chǎn)品的多維度圖像信息,結(jié)合光學(xué)傳感技術(shù)(如多光譜成像、3D結(jié)構(gòu)光)增強缺陷的可視化效果。算法層則采用輕量化設(shè)計,將模型推理速度壓縮至毫秒級,確保檢測節(jié)奏與產(chǎn)線速度的精準同步。更為關(guān)鍵的是,DLIA支持在線增量學(xué)習(xí),能夠根據(jù)新出現(xiàn)的缺陷類型動態(tài)調(diào)整模型參數(shù),從而持續(xù)適應(yīng)生產(chǎn)工藝的升級與產(chǎn)品迭代,實現(xiàn)了對缺陷特征的動態(tài)學(xué)習(xí)與自適應(yīng)優(yōu)化,從而在瞬息萬變的生產(chǎn)環(huán)境中維持檢測精度。
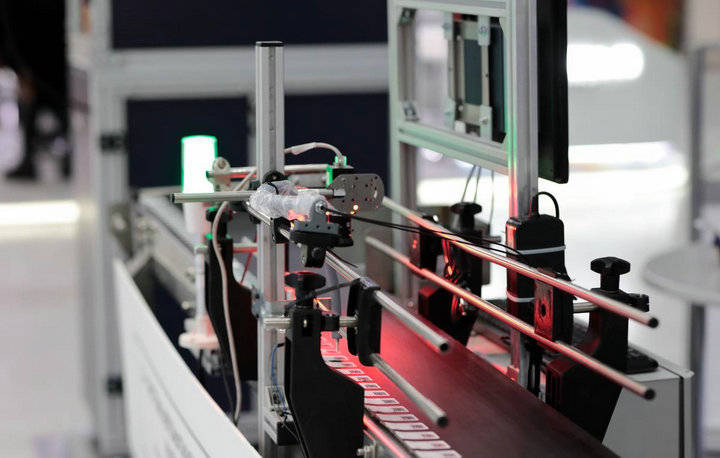
DLIA深度工業(yè)視覺檢測的價值,不單單只是替代人工目檢的執(zhí)行環(huán)節(jié),更為重要的是不再聚焦于成品階段的缺陷攔截的被動式管控,它可以轉(zhuǎn)為原材料、加工、裝配等全流程節(jié)點監(jiān)控。例如,在注塑成型過程中,可通過實時監(jiān)測模具溫度、材料流動狀態(tài)與產(chǎn)品形變數(shù)據(jù),預(yù)判氣泡或收縮缺陷的生成概率,并自動調(diào)整工藝參數(shù)以規(guī)避風(fēng)險;在精密焊接場景中,DLIA結(jié)合多模態(tài)的熱成像技術(shù)分析焊點溫度分布,提前識別虛焊、過焊等隱患,大幅降低廢品率與返工成本。
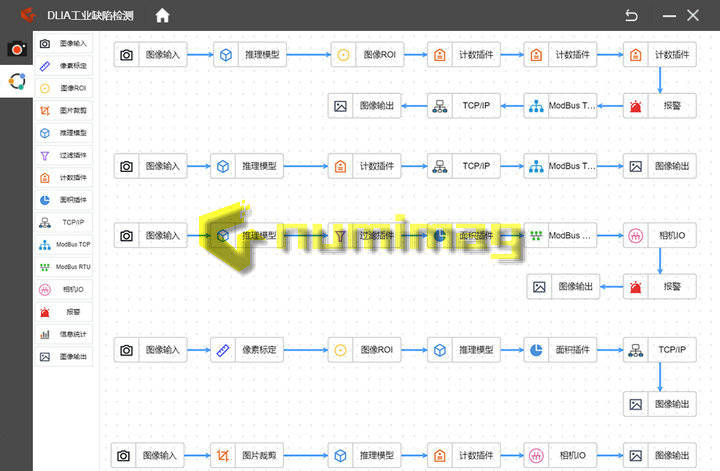
隨著多模態(tài)感知、邊緣計算等技術(shù)的成熟,未來的動態(tài)監(jiān)測系統(tǒng)將突破單一視覺維度,融合聲學(xué)、力學(xué)、熱學(xué)等多源信號,構(gòu)建更立體的缺陷表征模型。這場由DLIA引領(lǐng)的變革,本質(zhì)上是以數(shù)據(jù)為紐帶、以算法為引擎,重新定義工業(yè)生產(chǎn)的質(zhì)量基準。當機器視覺具備類人的感知與決策智慧,制造業(yè)的“零缺陷”愿景將不再遙不可及。而這一進程中,人工目檢的退場并非技術(shù)的勝利,而是人類智慧向更高維度躍遷的必然選擇。