在智能制造浪潮的推動下,DLIA工業(yè)缺陷檢測系統(tǒng)作為深度學(xué)習(xí)和機(jī)器視覺技術(shù)的集大成者,憑借其智能迭代能力與數(shù)據(jù)驅(qū)動邏輯,正在重構(gòu)工業(yè)的質(zhì)量檢測體系,為制造業(yè)的智能化轉(zhuǎn)型提供關(guān)鍵技術(shù)支撐。DLIA系統(tǒng)的核心突破在于突破了傳統(tǒng)機(jī)器視覺的靜態(tài)算法框架,解決了傳統(tǒng)檢測系統(tǒng)依賴人工預(yù)設(shè)規(guī)則,其本質(zhì)是對已知缺陷的有限枚舉,面對工業(yè)場景中復(fù)雜多變的缺陷特征時,往往陷入"識別維度單一"與"泛化能力不足"的困境。

DLIA缺陷檢測系統(tǒng)通過深度神經(jīng)網(wǎng)絡(luò)的自學(xué)習(xí)機(jī)制,構(gòu)建起動態(tài)演進(jìn)的缺陷認(rèn)知體系——系統(tǒng)通過初始模型對缺陷特征進(jìn)行基礎(chǔ)學(xué)習(xí),在實際運(yùn)行中持續(xù)吸收新增數(shù)據(jù)樣本,借助遷移學(xué)習(xí)技術(shù)實現(xiàn)模型參數(shù)的自主調(diào)優(yōu),使得系統(tǒng)的檢測精度隨著使用時間的延長呈現(xiàn)指數(shù)級提升,形成"越用越智能"的技術(shù)特性。
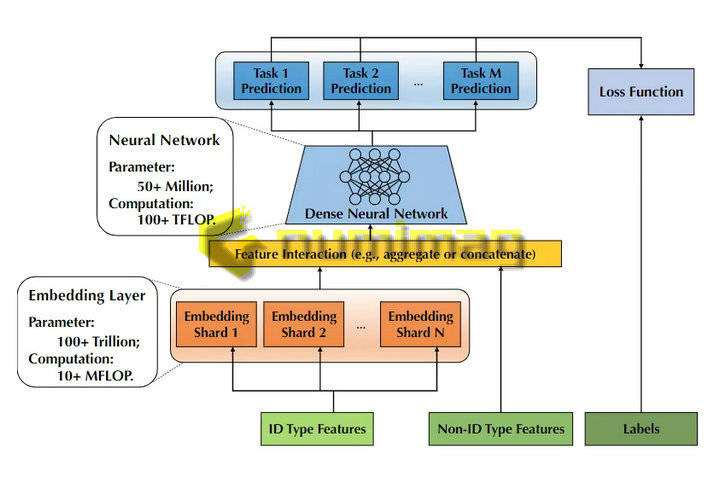
在工業(yè)質(zhì)量體系的構(gòu)建中,DLIA缺陷檢測系統(tǒng)的動態(tài)認(rèn)知能力很有戰(zhàn)略價值。傳統(tǒng)質(zhì)量控制的決策依據(jù)多基于歷史經(jīng)驗或抽樣統(tǒng)計,而DLIA系統(tǒng)通過全量數(shù)據(jù)的實時解析,能夠捕捉生產(chǎn)過程中微觀的異常波動。例如,當(dāng)原材料批次差異導(dǎo)致產(chǎn)品表面紋理變化時,系統(tǒng)可通過特征空間的非線性映射自動識別潛在風(fēng)險,而非依賴人工調(diào)整檢測閾值,使質(zhì)量管控從被動響應(yīng)升級為主動預(yù)測。
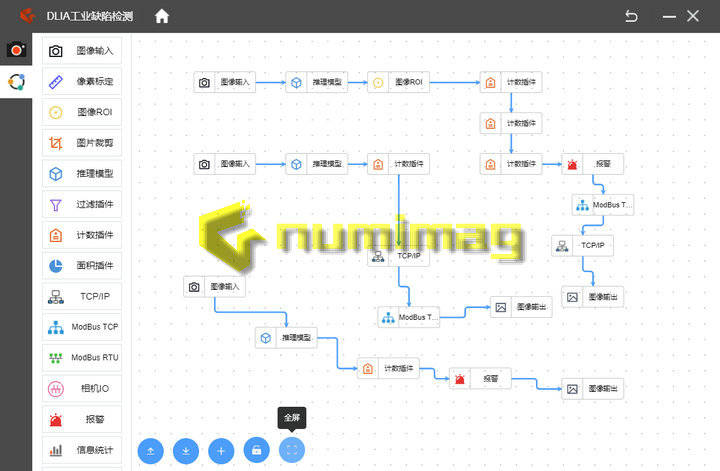
相較于早期僅作為獨(dú)立檢測單元存在的視覺系統(tǒng),DLIA缺陷檢測系統(tǒng)可以與多維度數(shù)據(jù)接口與生產(chǎn)控制系統(tǒng)、質(zhì)量管理系統(tǒng)(QMS)、企業(yè)資源計劃(ERP)等平臺實現(xiàn)無縫對接,讓檢測結(jié)果不再局限于"合格/不合格"的二元判斷,而是轉(zhuǎn)化為包含缺陷類型、空間分布、時序規(guī)律等維度的結(jié)構(gòu)化數(shù)據(jù)流,為質(zhì)量溯源、工藝優(yōu)化提供決策支持。當(dāng)質(zhì)量管控從成本中心轉(zhuǎn)化為數(shù)據(jù)資產(chǎn)的生產(chǎn)者,其戰(zhàn)略價值將獲得根本性重估,為制造業(yè)企業(yè)實現(xiàn)生產(chǎn)最優(yōu)化、流程最簡化、效率最大化目標(biāo)。