在全球制造業(yè)邁向智能化的進(jìn)程中,產(chǎn)品質(zhì)量始終是決定企業(yè)核心競(jìng)爭(zhēng)力的關(guān)鍵要素。面對(duì)復(fù)雜多變的工業(yè)場(chǎng)景,傳統(tǒng)檢測(cè)手段已難以滿足現(xiàn)代生產(chǎn)對(duì)精度、效率和適應(yīng)性的要求。DLIA深度視覺檢測(cè)系統(tǒng)以人工智能與機(jī)器視覺的深度融合,構(gòu)建起跨越物理邊界與工藝差異的全場(chǎng)景適配能力,為產(chǎn)品瑕疵識(shí)別提供了全新的技術(shù)范式。
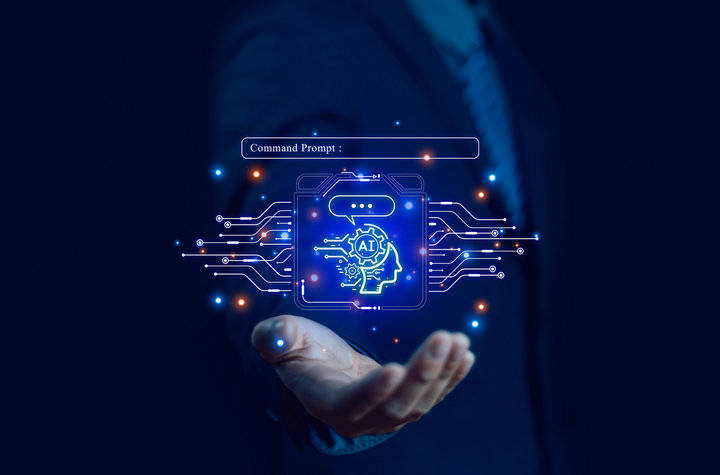
應(yīng)對(duì)產(chǎn)品瑕疵的多樣性挑戰(zhàn)時(shí),DLIA深度視覺檢測(cè)系統(tǒng)展現(xiàn)出超越傳統(tǒng)方法的認(rèn)知深度。工業(yè)生產(chǎn)中,瑕疵形態(tài)可能呈現(xiàn)幾何畸變、紋理異常、顏色偏移等多樣化特征,且隨著工藝迭代不斷演化。傳統(tǒng)算法基于人工定義的特征工程,難以覆蓋所有潛在缺陷類型。DLIA系統(tǒng)通過(guò)分層特征學(xué)習(xí)網(wǎng)絡(luò),建立起從微觀像素級(jí)特征到宏觀語(yǔ)義級(jí)特征的多尺度表征體系。這種層級(jí)遞進(jìn)的認(rèn)知結(jié)構(gòu),使其能夠捕捉到人眼難以察覺的亞像素級(jí)瑕疵,同時(shí)理解不同缺陷類型的工藝關(guān)聯(lián)性。當(dāng)面對(duì)新型未知缺陷時(shí),DLIA的在線學(xué)習(xí)模塊可自動(dòng)觸發(fā)模型更新,將檢測(cè)知識(shí)庫(kù)擴(kuò)展至新的領(lǐng)域,形成持續(xù)進(jìn)化的檢測(cè)能力。

面對(duì)工業(yè)場(chǎng)景的碎片化特征,DLIA深度視覺檢測(cè)系統(tǒng)同樣采用模塊化的架構(gòu)設(shè)計(jì)實(shí)現(xiàn)了靈活部署。其硬件接口支持與不同品牌、型號(hào)的工業(yè)相機(jī)、傳感器設(shè)備無(wú)縫對(duì)接,軟件層面則通過(guò)容器化技術(shù)封裝核心算法模塊。這種松耦合架構(gòu)允許企業(yè)根據(jù)產(chǎn)線特點(diǎn)自由組合檢測(cè)單元,既可在單機(jī)設(shè)備上實(shí)現(xiàn)局部質(zhì)檢,也能構(gòu)建覆蓋整條產(chǎn)線的分布式檢測(cè)網(wǎng)絡(luò)。在能源、半導(dǎo)體、汽車制造等差異化顯著的領(lǐng)域,也能通過(guò)配置不同的特征提取模塊與決策閾值,快速完成跨行業(yè)場(chǎng)景的適配,避免傳統(tǒng)方案需要定制開發(fā)的冗長(zhǎng)周期。

工業(yè)全場(chǎng)景適配不是簡(jiǎn)單的技術(shù)疊加,而是制造系統(tǒng)與智能技術(shù)的深度融合再造。DLIA深度視覺檢測(cè)系統(tǒng)通過(guò)構(gòu)建彈性化的檢測(cè)架構(gòu)、持續(xù)進(jìn)化的認(rèn)知能力和數(shù)據(jù)驅(qū)動(dòng)的閉環(huán)體系,正在重新定義工業(yè)質(zhì)檢的可能性邊界。這種變革不僅體現(xiàn)在瑕疵識(shí)別精度的數(shù)量級(jí)提升,更在于其開創(chuàng)了質(zhì)量管控模式從被動(dòng)響應(yīng)到主動(dòng)預(yù)防、從局部?jī)?yōu)化到全局協(xié)同的新范式。當(dāng)智能制造進(jìn)入深水區(qū),具備全場(chǎng)景適配能力的深度視覺系統(tǒng),必將成為推動(dòng)制造業(yè)高質(zhì)量發(fā)展的核心引擎。